AutoScheduler.ai Named Supply & Demand Chain Executive’s 2021 Top Supply Chain Project
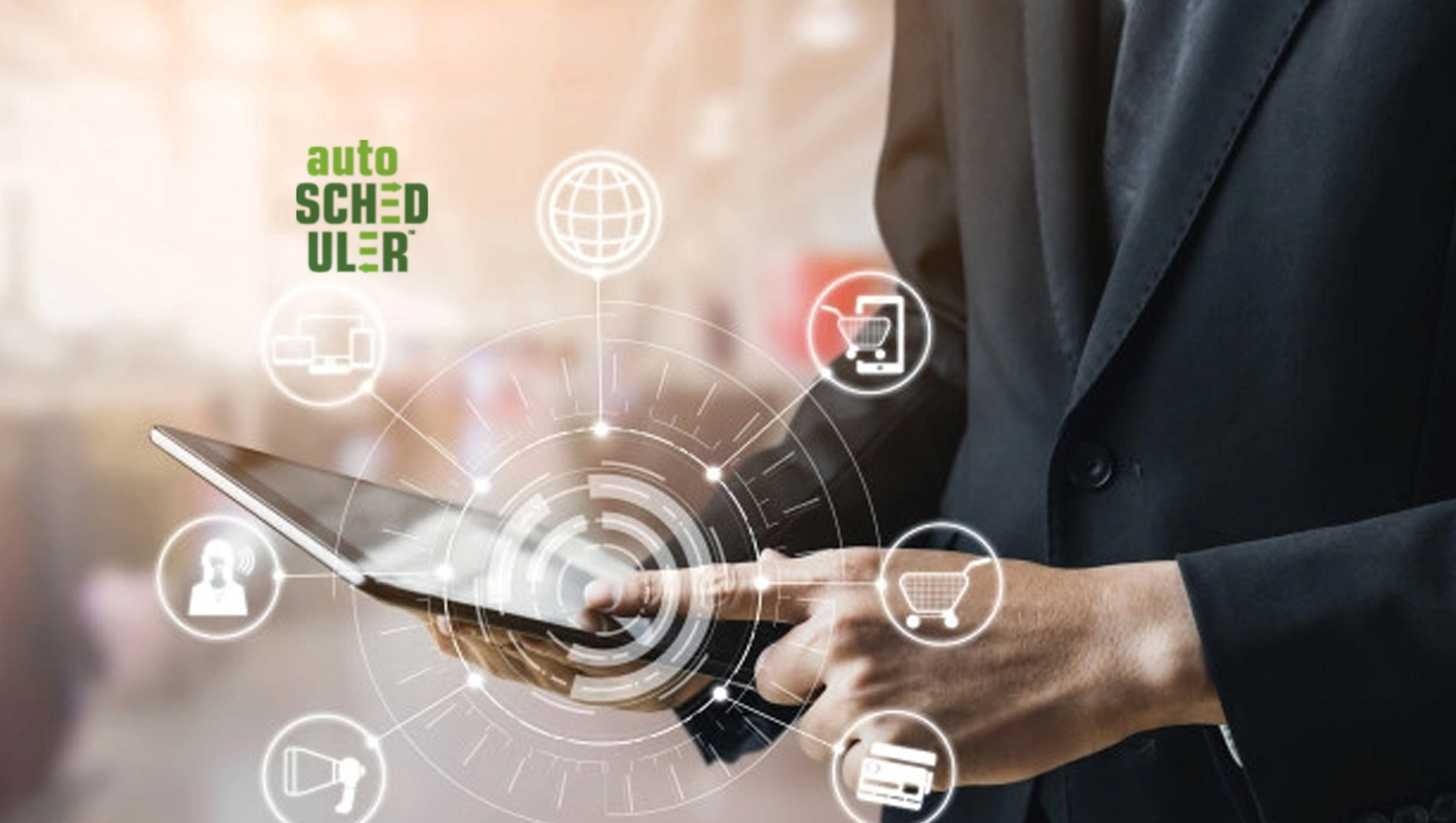
Automated Complex Planning Processes and Reduced Labor Capacity for a Savings Annually of Over $600,000
AutoScheduler.ai, an innovative Warehouse Management System (WMS) accelerator, announces the company has been selected as a recipient of the Top Supply Chain Projects Award for 2021 from Supply & Demand Chain Executive, the only publication covering the entire global supply chain. AutoScheduler was chosen for automating the complex planning process day over day at a large, global process manufacturer, significantly reducing the time needed for the planning team to create a dock schedule.
Read More: Hammerspace Named A 2021 Cool Vendor By Gartner
“We are honored to be recognized for this prestigious award,” said Keith Moore, Chief Product Officer, AutoScheduler.ai. “COVID brought significant challenges to this facility, and we were able to make a big difference with our solution, such as reducing the use of additional pallets and reducing labor capacity for over $600,000 in savings annually, along with numerous other benefits.”
“The supply chain industry has been challenged with a host of supply chain disruptions over the last year. Yet, the winners on this list continued to re-tool and innovate,” says Marina Mayer, editor for Supply & Demand Chain Executive and Food Logistics. “Whether it be moving a customer to a cloud-based solution or implementing a more sustainable shipping option, these top supply chain projects reflect the supply chain industry’s strength and resilience to overcome disruptions and work better, smarter, and more efficiently in the years ahead.”
The site had to add two overflow facilities for additional storage, very few carriers met appointment times, and the facility had high demand. Because of these things, along with the site’s high volume of case pick outbound shipments, they were struggling with coordinating all activities and often saw a massive number of repicked pallets for customer orders. To help resolve these challenges, the AutoScheduler solution was brought in to automate complex planning & orchestrate activities like inbound sequencing, bring-backs from outside facilities, replenishment, case pick, and loading sequences to ensure all shipments get out on time in full.
The results included:
- Reduction in the use of pallets, such as for re-picked orders, by appropriately sequencing in inbounds, replenishment, and picking to go from 27% pallets to 10% pallets over expectation. This equates to ~ five physical pallets reduced per load, saving $296,000 per year in asset costs.
- Reduction in the labor capacity required to perform repicks – Each repick took an employee 10 minutes to complete. The improved schedule is tracking to save over 14,000 hours in picking time alone, equating to a $325K labor cost reduction.
- Automated bring backs from the two overflow facilities, balancing inventory across all three buildings and ensuring customer demand is met with no service interruptions.
Read More: Virtual, Inc. Adds RFID Leader To Growing Technology Client Portfolio
The Top Supply Chain Projects (formerly known as SDCE 100) spotlights successful and innovative transformation projects that deliver bottom-line value to small, medium, and large enterprises across various supply chain functions. These projects show how supply chain solution and service providers help their customers and clients achieve supply chain excellence and prepare their supply chains for success.